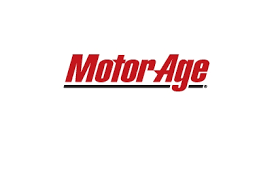
Productivity vs Efficiency
Motor Age Magazine
by Chris “Chubby” Frederick
When most of us started in the automotive repair business, we had a dream we were trying to achieve. It might have been spending more time with the family or with our hobbies. It might have been to earn more money to provide a better life, or we simply felt we could do it better than most. Whatever your dream was, the No. 1 dream wrecker I have witnessed in my 40-some years watching shop owners has been on the labor side of the business.
If you can succeed with productivity and efficiency, you will be much closer to your dreams coming true. This month, let’s listen to a lesson from our instructor on this subject, Randy Somers, while he explains to owners and service managers how to improve the labor side of your shop.
Many of us in the automotive profession have multiple names to describe virtually the same thing. For instance, a customer could have a check engine light on or a drivability concern and we could perform an engine diagnostic, or a checkout, an engine analysis or a test; we might even “pull codes.” Some of you might remember when we would scope the car to determine what was wrong. These terms used in different ways essentially mean the same thing to us. Productivity and efficiency are terms that are frequently used in different situations to describe the same thing.
Many shop owners measure productivity of techs something like this: “My techs seem busy all day.” Busy doesn’t always equate to being productive. Sometimes efficiency is expressed in these terms: “My tech is very efficient; he cleans all his tools after every job.” While that could be one interpretation of efficiency, it isn’t the definition we are using here. Productivity, or lack of it, is an issue many people face in the day-to-day world of owning a shop. Over the years, I have heard owners saying things like “I don’t know what’s wrong, everyone seems to be busy and nobody is goofing off. We must need more cars.”
In order to be profitable and offer customers great service with the WOW factor, a shop needs to be truly productive and efficient. Here are a few simple steps to follow to get you well on your way.
The Difference
First we must define the terms. To me, technician efficiency is measured in this way: If I give a technician a one-hour job that he or she does in one-half hour, then that tech is 200 percent efficient. My experience in automotive is that most technicians are efficient. When you give them a one-hour job they are usually done in one hour. Sometimes even less. Productivity is a measure of how many of those efficient jobs get stacked on top of each other in an eight-hour day to make eight hours of labor sales or more. Keeping that thought in mind, we should always be 100 percent productive or more than 100 percent if our technicians are over 100 percent efficient. So why aren’t we?
The second step will be to determine where we are in terms of productivity versus where we should be in productivity, which is different again from where we could be. To measure your overall team productivity, you need to take the total labor hours produced in any given time period divided by the total hours of floor time or actual clock hours worked in the same time period. For example, if I have 90 hours of billed labor in a week and my techs have 120 hours of actual time worked (3 techs x 40 hours),then I would be 75 percent productive.
Realistic versus Achievable
The third step would be to determine what a realistic and achievable goal for productivity is. Being 75 percent productive, is that a good number or not? I can tell you that it is above the industry average. Is 75 percent a good number or not though, that is a different question altogether. I would never shoot for the average. No one ever wakes up in the morning and says “Wow, I hope I have an average day today.”
People usually don’t fail because they set the bar too high, people usually fail because they set the bar low and achieve their goal. In order to know if 75 percent productive is good or not, you need to know what you are capable of producing. In the above example, it would be easy to say that if my techs work 120 hours then I would expect 120 hours. If I set the bar high, I might even expect 120 percent productivity or 144 hours of labor in a 120-hour week. This is achievable but probably not sustainable.
I think that 90 percent is a good target for productivity. It is realistic, attainable and sustainable. Once we reach 90 percent productivity, I would recommend adding another tech and making them 90 percent productive as well. If we agree that 90 percent productivity is a good target or goal, we have to ask ourselves, 90 percent of what? Ninety percent of 120 hours of floor time would be 108 hours produced. That works if we assume all techs are capable of producing 40 hours in a 40-hour week.
Is a typical A level technician capable of producing 40 hours in a 40-hour week? I think so. Is a typical B level technician capable of producing 40 hours of labor in a 40-hour week? I think so. Is a general service tech capable of 40 hours in a 40-hour week? Ehhh. Maybe 20 is a more realistic number in this example. So do I really have the capability to produce 120 hours in 120 hours worked, or am I staffed to produce 100 hours in a 120-hour week? If that is the case, then that would make 90 percent productivity 90 hours billed, not 108.
Diagnosis the Problem
The last step will be to figure out exactly where the problem lies if your technicians aren’t at least 90 percent productive. It is easy to blame “those dang technicians” when productivity is low. The problem is that — as the above definition shows — efficiency is more of a technician issue, not productivity. Low productivity is more a front counter function than a technician concern.
So now it’s “those dang service writers’ fault.” While that might be satisfying to say from time to time, it isn’t always true either. In order to fix productivity, we need to determine what is stopping us from being productive. Let’s examine some of the many things that get in the way of productivity.
Technician efficiency could be a cause of low productivity, so what hinders efficiency in technicians? Technician skill level could stand in the way of our being productive. Are we dispatching the correct skill level work to the correctly skilled technicians? Do we have a training issue or even a retraining issue? Are technicians being pulled on and off of vehicles and that prevents them from being productive? Are the technicians standing around waiting for parts, or could they possibly be standing around waiting for okays on the work they have already checked out (the result of a backlog at the front counter)? Are they waiting for someone to direct them to what to work on next, or have we set expectations so they already know which jobs to work on next? Is it a car count concern, or is it a concern with the amount of work we recommend on each vehicle? It can make your head spin trying to decipher all the reasons that could prevent us from being both efficient and productive.