How to Inspect Ball Joint Wear Due to Friction
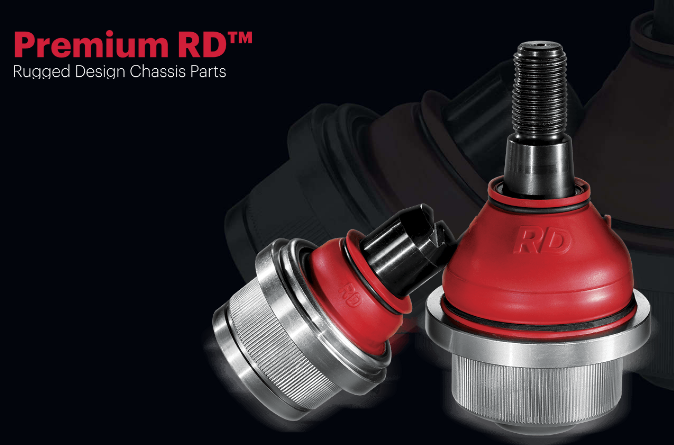
One of the main reasons ball joints can fail is from excessive wear from friction. Techs often have a problem locating valid specs for ball joint testing. This allows for consideration of the real-world effects that cumulative bushing and ball joint wear have on the steering and suspension system as a whole. If you use a pry bar and brute strength, your inspection could be influenced by the bushings in the control arms.
Visual inspection
Boot seal designs and materials have improved over the past two decades. But, they are still prone to damage. If you see a damaged boot, chances are the stud and internal surfaces are already damaged. Wear occurs when water and small bits of debris make their way past the boot. Damage can also be accelerated when the grease escapes and leaves the joint dry. Most of the OE joints don’t have a Zerk fitting, so the debris can’t be flushed out of the joint.
Some ball joints that are equipped with a grease fitting use the fitting as a wear indicator. If a grease gun will not couple to the fitting, the joint needs to be replaced. As the joint wears, the Belleville washer or spring maintains the tension on the bearings to maintain zero axial end play as the control arms move. Lateral wear causes the ball stud to move inside the bearing and can affect camber and tire wear. The Belleville washer or spring will not compensate for lateral wear.
Ball joint inspection
Loaded Joint: To check a loaded ball joint, place a jack or jack stand under the lower control arm to support the weight of the vehicle. Attach a dial indicator to the lower control arm and locate the dial in a vertical position to measure axial runout at the steering knuckle. In the case of an AWD front ride strut or independent RWD, it may be necessary to mount the dial at the CV joint. Moving the steering knuckle can help check lateral runout. The upper joint is loaded in a SLA suspension that has the coil spring over the top arm. To check the joint, support the upper control arm to unload the joint. If the ball joint has a built-in wear indicator, joint play should be checked while the vehicle is on its wheels.
Follower Joint: To assess a follower-type joint, the Belleville washer or spring is loaded or compressed to check for axial end play. For a strut-type suspension, place a jack stand under the cradle to allow the strut to fully extend. Attach the dial indicator clamp to the lower control arm and locate the dial in a vertical position to measure axial runout at the steering knuckle. Place a jack under the ball joint and load the joint by raising the jack. Turn the steering wheel and observe the ball joint to check lateral runout.
For a SLA suspension, the upper control arm can be blocked and the joint can be compressed. Attach a dial indicator to the steering knuckle and locate it in a vertical or parallel position to measure axial runout at the lower control arm. Moving the steering knuckle can check lateral runout.
The overall condition of the chassis is important to the safety and performance of the vehicle, so heed the specifications for alignment, ride height and ball joint end play.
Post adapted from the article Ball Joint Friction and Wear – Brakeandfrontdend.com